Unlocking the Power of Welding WPS: Techniques for Effectiveness and Security in Manufacture
In the world of fabrication, Welding Treatment Specifications (WPS) stand as the backbone of welding procedures, dictating the necessary steps for achieving both performance and security in the manufacture procedure. Comprehending the complexities of WPS is paramount to utilizing its full capacity, yet lots of companies struggle to open truth power that exists within these papers (welding WPS). By diving into the approaches that enhance welding WPS, a globe of boosted performance and heightened safety and security awaits those happy to discover the subtleties of this vital aspect of fabrication

Significance of Welding WPS
The value of Welding Procedure Specs (WPS) in the manufacture sector can not be overstated. WPS function as an important roadmap that details the required steps to ensure welds are executed consistently and correctly. By defining vital criteria such as welding processes, materials, joint layouts, preheat temperatures, interpass temperatures, filler steels, and post-weld warm treatment demands, WPS offer a standardized method to welding that enhances effectiveness, top quality, and security in construction processes.
Adherence to WPS aids in achieving harmony in weld high quality, minimizing the likelihood of flaws or structural failures. This standardization likewise assists in conformity with market guidelines and codes, ensuring that made frameworks meet the called for safety standards. Additionally, WPS paperwork enables welders to replicate effective welding procedures, leading to regular results throughout different projects.
In significance, the thorough development and rigorous adherence to Welding Procedure Requirements are extremely important for maintaining the stability of welded structures, protecting versus potential dangers, and promoting the online reputation of fabrication firms for supplying top notch products and services.
Secret Aspects of Welding WPS
Enhancing Performance With WPS
When maximizing welding procedures, leveraging the key elements detailed in Welding Procedure Requirements (WPS) comes from this source to be essential for taking full advantage of and streamlining processes efficiency. One method to boost efficiency with WPS is by meticulously picking the ideal welding specifications.
Additionally, appropriate training and certification of welders in understanding and implementing WPS can better boost performance. Guaranteeing that all group members are well-versed in translating and implementing the WPS accurately can remodel and lessen mistakes, conserving both time and sources. Regularly examining and upgrading the WPS to include any lessons found click to read out or technological advancements can also add to performance improvements in welding procedures. By embracing the standards set forth in the WPS and continuously seeking means to maximize procedures, makers can attain greater efficiency degrees and exceptional outcome.
Ensuring Safety in Fabrication
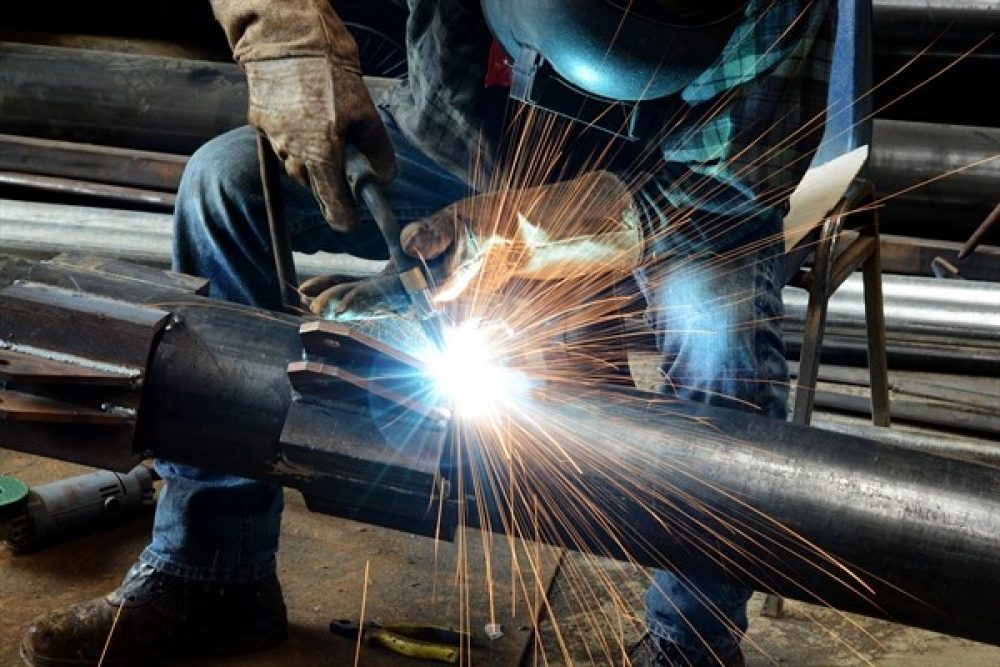
Security methods in fabrication play a pivotal function in safeguarding workers and enhancing functional procedures. Making sure safety in manufacture includes a diverse technique that includes numerous facets of the welding procedure. One fundamental element is the provision of personal safety tools (PPE) customized to the specific threats present in the construction atmosphere. Welders have to be furnished with ideal gear such as helmets, handwear covers, and protective garments to reduce threats connected with welding tasks.
Moreover, adherence to appropriate ventilation and fume removal systems is crucial in maintaining a healthy and balanced workplace. Welding fumes include hazardous substances that, if breathed in, can pose significant health risks. Carrying out efficient ventilation steps aids to lessen direct exposure to these hazardous fumes, promoting breathing wellness amongst workers.
Regular devices upkeep and evaluations are additionally necessary for making sure safety and security in fabrication. Malfunctioning equipment can lead to mishaps and injuries, emphasizing the importance of timely fixings and regular checks. By focusing on safety and security actions and fostering a culture of recognition, construction centers can develop a productive and secure work setting for their personnel.
Implementing WPS Ideal Practices
To enhance functional efficiency and guarantee quality end results in construction processes, integrating Welding Procedure Specification (WPS) ideal techniques is paramount. Picking the proper welding process, filler product, and preheat temperature level defined in the WPS is critical for achieving the preferred weld quality. Making certain that qualified welders with the required accreditations lug out the welding treatments according to the WPS standards is essential for uniformity and dependability.
Verdict
Finally, welding WPS plays an essential duty in ensuring effectiveness and security in construction procedures. By concentrating on essential aspects, enhancing performance, and carrying out best methods, firms can optimize their welding operations. It is vital to focus on safety and security actions to stop crashes and ensure a smooth production process. By complying with these approaches, businesses can unlock the complete possibility of welding WPS in their fabrication operations.
In the realm of fabrication, Welding Treatment Requirements (WPS) stand as the foundation of welding procedures, determining the needed actions for accomplishing both effectiveness and safety in the fabrication process. By specifying crucial criteria such as welding procedures, products, joint styles, site link preheat temperatures, interpass temperatures, filler steels, and post-weld warmth therapy demands, WPS offer a standardized approach to welding that boosts performance, high quality, and security in fabrication procedures.
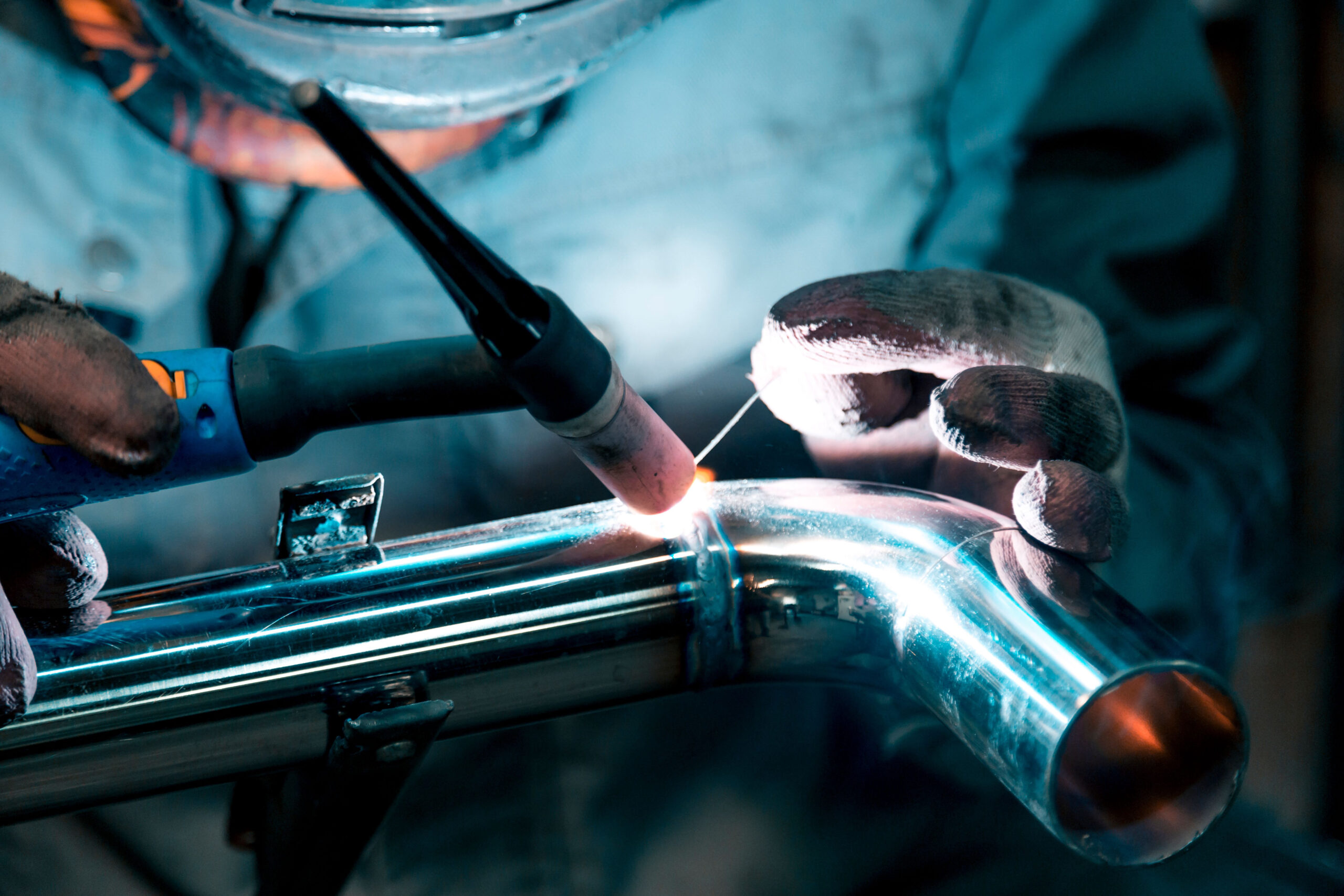
When optimizing welding operations, leveraging the crucial elements described in Welding Treatment Requirements (WPS) becomes necessary for making the most of and enhancing procedures productivity. (welding WPS)
Comments on “Developing a Welding WPS: Step-by-Step Recommendations for Professionals”